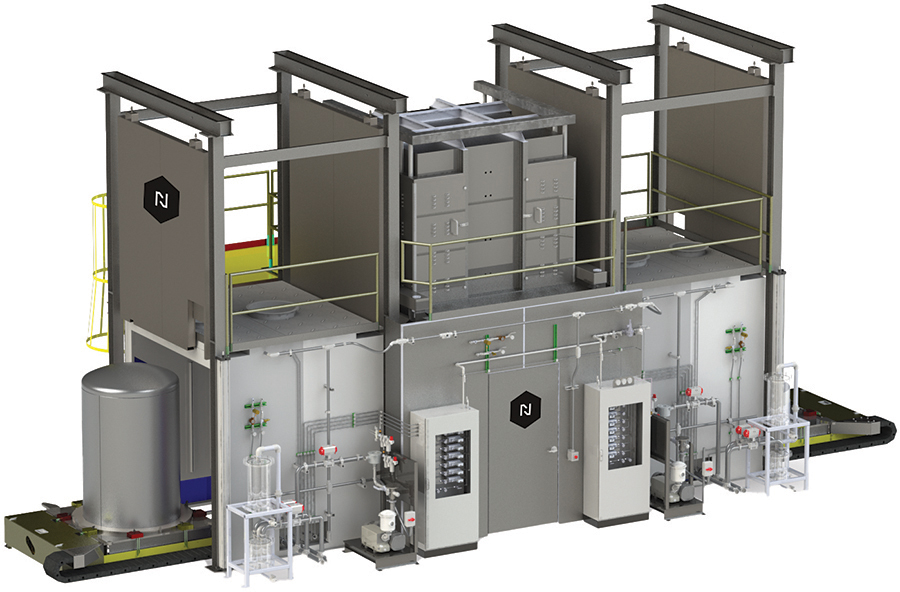
Nitrex has announced its newest order for two vapor phase aluminizing furnaces to a leading jet engine manufacturer who is scaling up production of high-performance blades and vanes.
In a move aimed at elevating its manufacturing capabilities, a leading jet engine manufacturer and a loyal repeat customer of G-M Enterprises, a Nitrex company, is gearing up to integrate two cutting-edge vapor phase aluminizing (VPA) coating furnaces during the first half of 2024. This strategic investment not only marks a bold step forward in the company’s ongoing commitment to advancing aerospace manufacturing but highlights a continued partnership that has seen the customer acquire various types of Nitrex vacuum furnaces for multiple locations.
These high-capacity, low-maintenance automated retort VPA furnaces are purposefully engineered with moving bases and a fixed heat chamber, enhancing operational efficiency. Each retort is seamlessly sealed to the moving bases, allowing for concurrent handling of two loads, each containing three coating cans. The result is a streamlined process that runs two cycles back-to-back, completing the treatment within just over 24 hours. The automated furnace supports unattended start-ups, empowering operators to focus on preparing loads for the second system which facilitates concurrent operations for heightened productivity.
“Our VPA furnaces ensure seamless operations, providing our customer with a competitive edge in production capacity,” said Robert Huckins, national sales manager. “This is crucial in meeting escalating demand while delivering high-performance and longer-lasting blades and vanes vital for high-temperature fired engines.”
A standout feature of the Nitrex VPA design is the raised fixed heat chamber, effectively shielding operators and the furnace room against potential heat exposure. This innovation eliminates the need for cumbersome protective heat suits. The hot retort remains securely housed within the insulated furnace, prioritizing operator well-being. Furthermore, this safety measure confines the load base and retort/coating load within the SAR/VPA furnace housing until the retort temperature drops below 150°C (300°F). This meticulous attention to safety underlines the commitment to operational excellence throughout the entire process.
This strategic investment not only underscores the manufacturer’s commitment to staying at the forefront of technological advancements but also solidifies a lasting partnership, showcasing the mutual trust built over multiple acquisitions of various vacuum furnaces.
MORE INFO www.nitrex.com