A plethora of expertise makes up the complex products and services offered by Morgan Advanced Materials, but it essentially boils down to a simple concept: helping its customers achieve more with less.
However, when you look at the vast amount of what customers can get through Morgan Advanced Materials, the bottom line might almost seem like a paradox.
“From an external perspective, we would be viewed as a world leader in advanced material science and engineering of ceramics, carbon, and composite materials,” said Holly Hulse, president of the Thermal Products Division at Morgan. “We operate in a number of well-defined markets, and our applications expertise offers customers a valuable differentiator. We bring highly-engineered specified materials, components, and sub-assembly parts, so that when our customers have a challenging technical problem, we work with them to solve it with our engineering combined with our materials.”
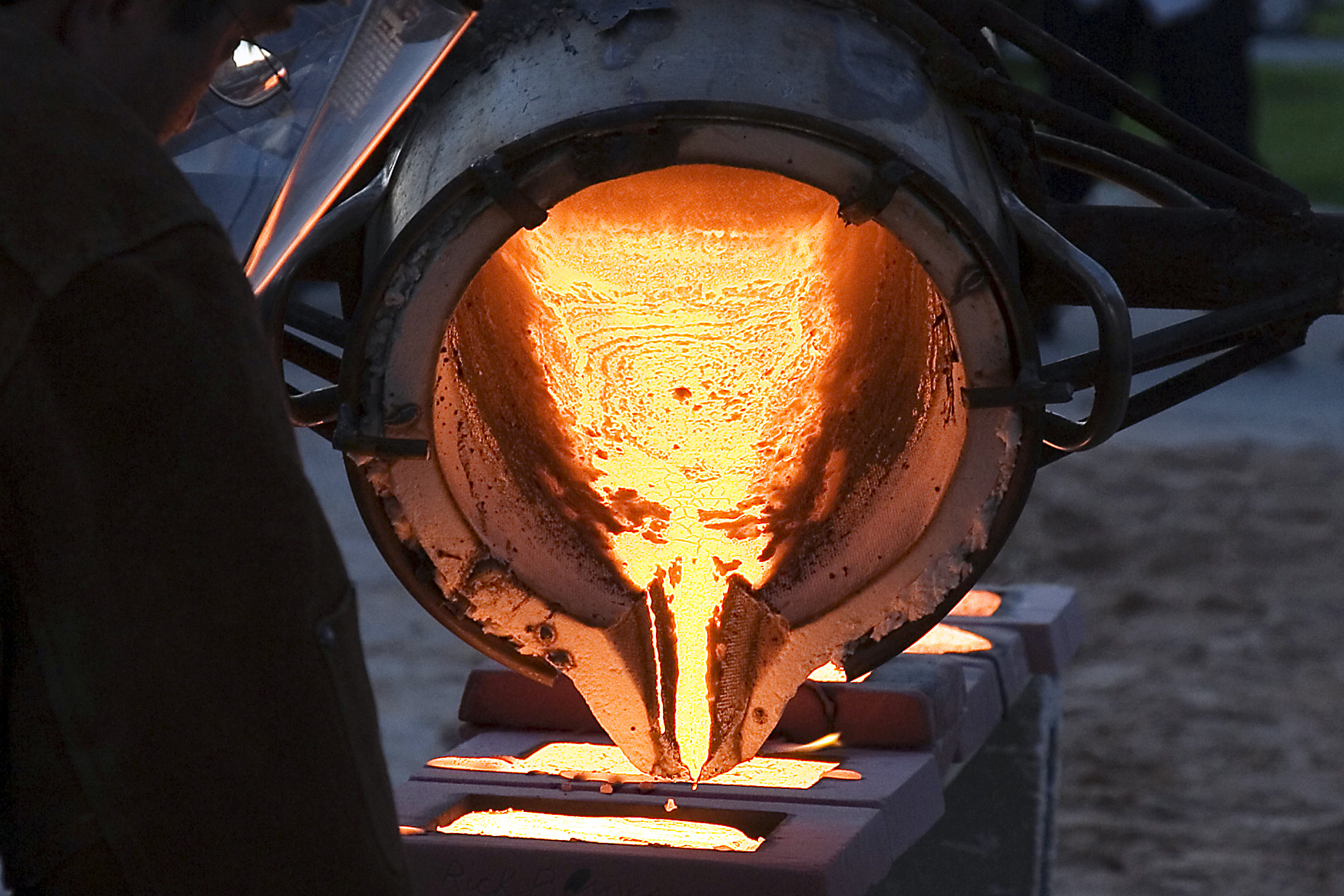
Product range
Morgan’s principle product range involves insulating fibers and electrical carbon systems, according to Hulse.
“We have businesses all about seals and bearings, ceramic cores, and — back to our roots — the crucibles for metal processing,” she said. “We also do a number of different customized materials that are application specific. When a customer has a specific need, we can go to them with a kind of bespoke solution.”
Morgan offers its products and services to a range of industries: healthcare, petro-chemical, transportation, electronics, energy, security, and other industrial industries, according to Hulse.
“I think one of the unique things for us is that a lot of our products are required to perform critical duties in a very harsh or demanding operating environments,” she said.
And a part of what Morgan does involves its Thermal Products Division, which is made up of two businesses.
“One of them is the Thermal Ceramics business, and the other is the Molten Metal Systems business,” Hulse said. “On the other side of the house, we have our Carbon and Technical Ceramics division, which has three parts; Electrical Carbon, Seals and Bearings, and a Technical Ceramics business.”
Thermal ceramics
Morgan’s Thermal Products Division targets thermal ceramics in particular, according to Hulse.
“In this business, we’re manufacturing an extensive range of high-temperature insulation products and systems that provide thermal insulation in high-temperature environments, sometimes corrosive environments,” she said. “Our primary focus is high-temperature insulation and the products within that, which include insulating fiber, fire-brick, and monolithic products. And the reason that people use our products is that we help them to reduce the energy consumption in their processes.”
Hulse noted Morgan’s products are well known for helping customers that have high-energy processes in order to reduce energy consumption, emissions, and operating costs.
“When we come in, the value proposition we have is much more than just an individual product,” she said. “We’re working with them on a solution to help them solve their operating challenges and to run more efficiently.”

Global footprint
To be able to meet all the challenges customers present, Thermal Ceramics has 36 manufacturing sites across five continents where it makes insulating fiber, fire brick, and a range of microporous products — thinner, lightweight solutions used in specialty applications in aerospace, for example.
“In aerospace, insulating fiber products tend to be a little bulkier,” Hulse said. “The microporous products are condensed and, as a result, bring you very high performance but with minimal real estate.”
Microporous products are perfect for performance-critical applications where insulation space is at a premium and overall weight must be minimized, according to Hulse.
“They provide a tremendous benefit,” she said.
Microporous heat-treat applications
Microporous products also are extremely beneficial in heat-treat applications as well, according to Hulse.
“If you think about a furnace, they can often be used as a backup insulation,” she said. “Instead of having a thick backup insulation and reducing the total capacity of the kiln, by putting in a very thin layer of the microporous material, you can get some of the same benefits but in a smaller space, so you have more room to move your products.”
Protecting the environment
Thermal Ceramics’ range of products is designed to be environmentally conscious, according to Hulse.
“Morgan is focused on environmental health and safety, and we believe that flows into the products we have,” she said. “When we look at the cost of energy increasing and we also see that there are more and more people focused on environmental concerns, we believe that the products we bring will allow our customers to run their plants in a more environmentally friendly way. We are looking to bring new and innovative alternative products, and we have been the leader in introducing low biopersistent products over the years to try to stay ahead of the needs — and the market — as the regulations continuously tighten.”
An example of that falls a bit outside the realm of heat treatment and with Morgan’s work with catalytic converters in vehicles.
“We have a number of different products that are used in holding in the heat, reducing the space, etc., to meet increasing emissions legislation, and in the heat-treatment arena, with increasing pressure on carbon dioxide and sulfur dioxide emissions, we can play a key role with our customers in enabling that,” Hulse said.
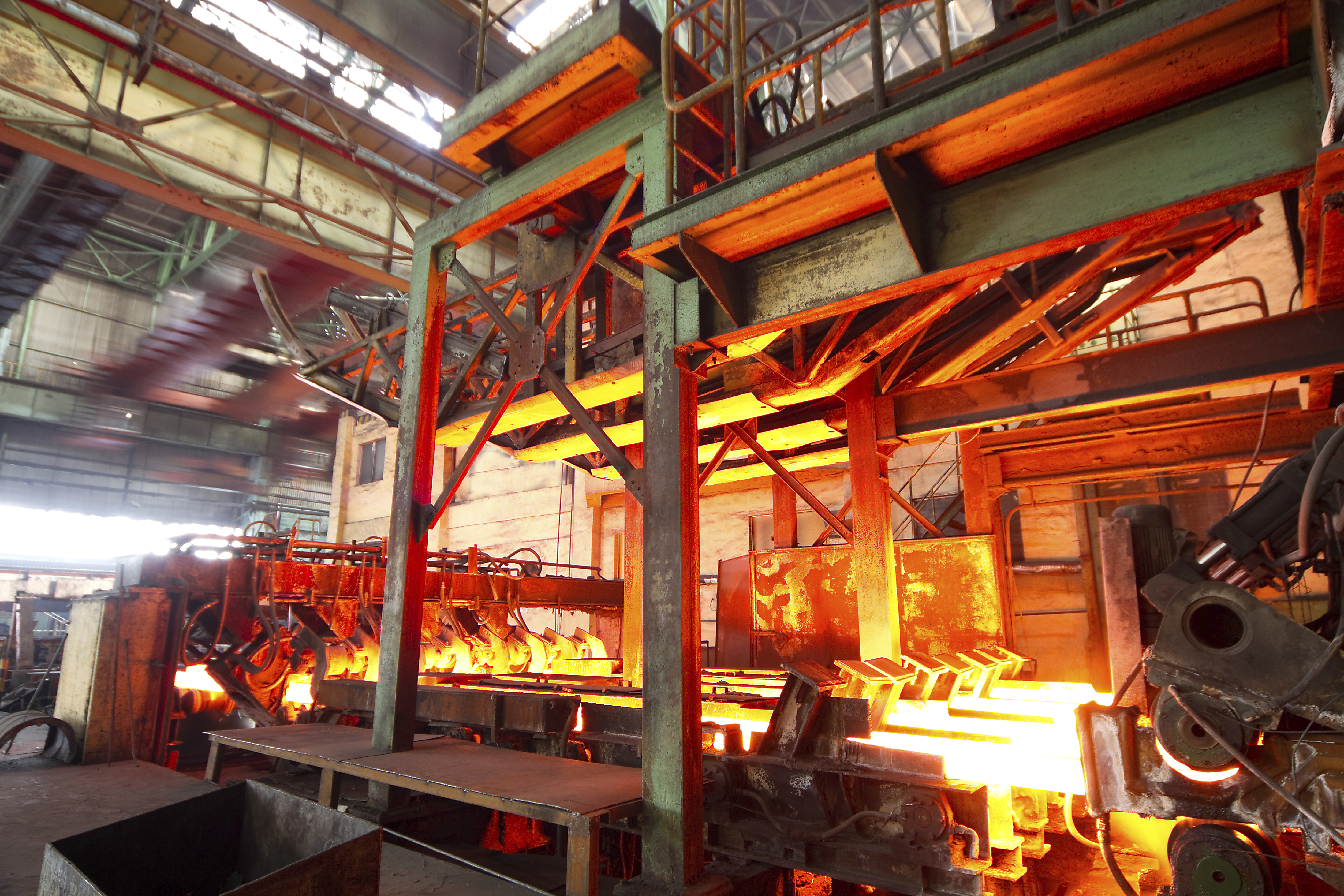
Worldwide expertise
Morgan’s global footprint enables the company to supply a customer’s needs anywhere in the world, which means local and global expertise that Morgan can leverage, which Hulse is keen to demonstrate.
“We have a wide range of engineering capabilities; we have specialist engineering teams; we have installation support to help to not only design the solution but also to help with the installation and the actual running of it,” she said. “We have the ability to support on assessing how the heat-treatment equipment is working, whether it’s through using infrared cameras to assess the condition of the equipment or just to help with the profiles at which we run the equipment. We have the technical knowhow, and we also have dedicated research and development to bring on new and improved products to the market continuously.”
Finding high-tech and innovative solutions to its customers’ problems are, ultimately, what makes Morgan tick, according to Hulse.
“This is an end business for us; this is the core of who we are,” she said. “We get very excited and probably a little nerdy about how we approach these challenges.”
Through its extensive product portfolio and worldwide facilities, Morgan has adopted a leading position within the fields of international projects such as CPI, iron and steel, and power generation.
“We have the ability to successfully apply single-order sourcing across the barriers of cultural understanding, language differences, international trading, and border control,” Hulse said. “We have so much experience that we give our customers a sense of confidence and trust. And that further strengthens our international positioning.”
‘Tailored solutions’
A recurring theme that runs throughout Morgan is what Hulse calls “tailored solutions.”
“It applies to our engineering services, which provide carefully tailored combinations of our products to meet a specific need, all the way through to R&D, which is familiar with working with major industries and universities to produce new technology required by tomorrow’s industry,” she said. “I think it’s a combination of: what do we do in the short term, and how do we make sure that we take time to leverage our previous experience but listen to specific current needs and future needs of our customers? Then we leverage the necessary R&D and the engineering services and our broad cultural and global footprint to really serve their needs and meet them where they are — making it easy for them to achieve their goals.”
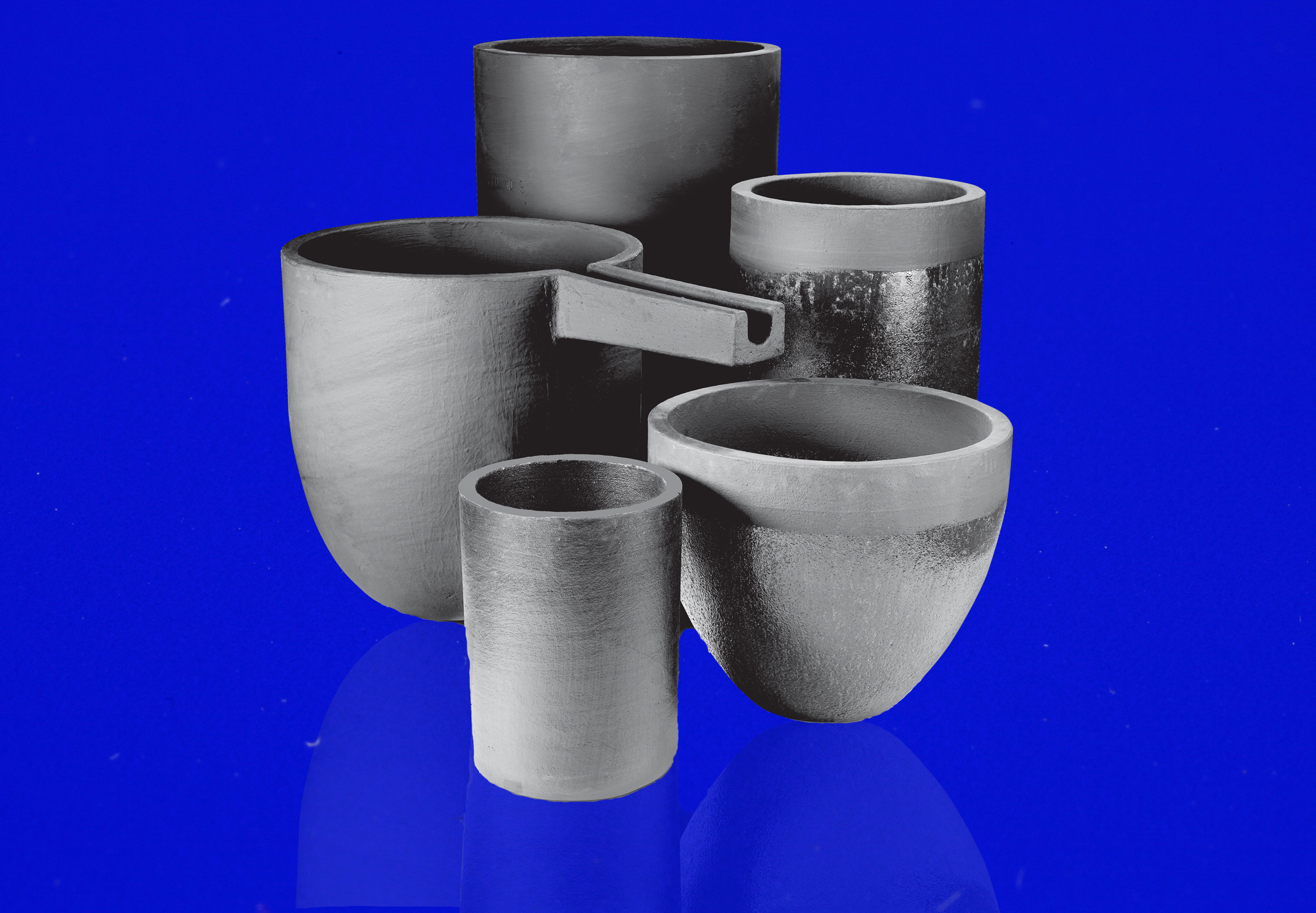
Morgan Advanced Materials
Morgan backs up that promise of guaranteeing a solution with 163 years of experience.
Morgan began in 1856 as Morgan Crucible, and after more than 160 years of continuous trading, Hulse said Morgan continues to operate in the same space it started in, although it’s obviously expanded in many directions since then. The company is now officially known as Morgan Advanced Materials, a PLC headquartered in Windsor, U.K., listed on the London Stock Exchange.
“Our purpose is to use advanced materials to help make more efficient use of the world’s resources, and to improve the quality of life,” she said. “All of it comes down to the engineering of high-performance materials and specialized products that go after reliable solutions to the technical challenges that our customers have. We can help our customers achieve more with less.”
Despite Morgan’s continuing innovations, Hulse emphasized the company’s most fundamental product is still the crucible.
“I’m pretty proud of that,” she said. “We haven’t walked away from our core; we’ve built on it. And with thermal ceramics, we have been the one that has continuously revolutionized the high-temperature insulation market. That’s been ongoing since the 1990s when we introduced Superwool® low biopersistent fiber technology. And now we have introduced Superwool XTRA® fiber, the latest in this family, a breakthrough technology as this particular material has no crystalline silica formation.”
Finding solutions to future problems
Morgan is always striving to stay ahead of the curve, to stay ahead of requirements and make sure the company is finding solutions to its customers’ future problems, according to Hulse.
“I’m very proud of that, and the team is so committed to continuously look for new ways to meet the needs of the customers and partner with them to enable their success,” she said.
As Morgan drives forward in its second century of business, Hulse said Morgan is diligent in its mission to supply thermally efficient lining in order to heighten the demand of energy while lowering carbon dioxide emissions.
“That’s going to mean that we have to develop more and more precise solutions to meet the heat-treatment needs,” she said. “Government agencies are laying on more requirements for our customers, and we all try to do well by the world in which we live. We believe that we can make a difference there by helping to anticipate those needs and then really helping to save energy and to reduce the emissions output. I think there are companies who have already recognized us for this, and we’ve been partnering with some of them for a long time.”
With that in mind, Morgan will continue to offer its customers the best solutions to meet all their needs, according to Hulse.
“It doesn’t sound like a sexy business from the outside, but I think that we’re doing some really revolutionary things with a product that’s been around for a very long time, and we’re continuously striving to make it new and fresh and better performing,” she said. “I’m really delighted to see where we’ve come from. We have more in our bag to unveil over the next couple of years, and we’re going to continuously be pushing to have the solutions available as our customers need them.”
More info www.morganthemalceramics.com